Method Statement for Asphalt Paving Works | Asphalt Concrete | Asphalt Pavement Construction | Asphalt Road Construction | Highway Pavement
In this article we will discuss about Method Statement for Asphalt Paving Works | Asphalt Concrete | Asphalt Pavement Construction | Asphalt Road Construction | Highway Pavement.
The scope of work of this method statement is to describe the responsibilities of personnel involved, execution procedure, safety factors and documents to be recorded for Asphalt Paving Works
Title:
Method Statement for Asphalt Paving Works are given below: Asphalt Concrete
Scope:
The scope of work of this method statement is to describe the responsibilities of personnel involved, execution procedure, safety factors and documents to be recorded for Asphalt Paving Works. Asphalt Road Construction
OTHER POSTS:
-
Method Statement for Installation of Anchor Bolts | Setting Out
-
Method Statement for Formwork, Reinforcement and Concrete Works
-
Method Statement for Concrete Repair Works | Structural Works
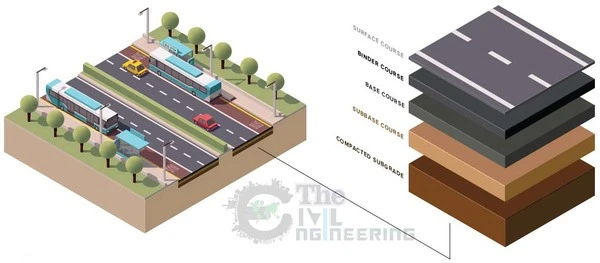
Relevant Process/Specifications:
Tender Specifications Asphalt Concrete
Responsibility:
The Construction Manager/Project Engineer is responsible for the asphalt paving works. Highway Pavement
The Civil Construction Contractor’s Safety Officer shall ensure that necessary work permits are availed before the work commences and that the work is carrying out in safe manner. Highway Pavement
The responsibility of the survey activities lies with asphalt paving work subcontractor. The survey team of civil construction contractor shall verify the data frequently. Asphalt Concrete
Inspection and testing activities shall be controlled by the QC Engineer of Civil Construction Contract or through the site laboratory of Company.
Equipment:
- Shovel
- Compaction Roller Machine
- Spreader
- Trucks
- Sprit Level
- Plumb bob
- Electric air blower/Air Compressor for cleaning Asphalt Road Construction
- Drilling Machine
- Hammer
- Measuring Tapes
- Markers
Execution: Procedure for laying Asphalt road works
Surface Preparation:
- The surveyor shall mark the road center line and width of the embankment prior to starting of any road works; The CONTRACTOR shall make detail survey of the existing services (If any) by the side of the road or crossing the road.
- Surveyor shall make a survey report for the existing levels prior to filling or cutting and engineer should make sure for the same.
- All the road works and road crossings must be executed as per the approved drawings and as per project specifications.
Road embankment:
- Embankment shall be installed on top of the existing natural ground, thickness of this layer shall be at least 30 cm.
- Material to be used for road embankment shall be A-1-a OR A 1-b or A-2-4 in accordance with AASHTO classification.
- Every layer should be compacted with heavy compactor and the compacted density of the soil shall be equal to or greater than 95% M.D.D., with no single value below 92%.
Sub Grade:
- Ensure that approved sub-grade material is used and the material sample shall be collected and tested as per project specifications upon receiving of material at site. Highway Pavement
- Sub-grade material shall be placed above embankment filling
- The approved Sub-grade material shall be backfilled to the thickness of 300mm and it should backfilled in two layers (each layer 150mm ).
- Compaction of sub-grade shall be facilitated by means of a 10-12 ton roller, rolling shall be continue to achieve the MDD of 98% as per approve drawings and project specifications.
- Thickness of sub-grade shall not be less 300mm as specified in the approved drawings
- The formation shall be shaped and graded to an even and uniform, well filled surface, shaped similarly to the finished surface of the road.
- Compaction test shall be done by approved laboratory for the Sub grade.
Laying of Curbstones:
- The above work shall be carried out according to the Method statement of Kerbstones.
- Laying of kerb stone shal I be inspected and approved by 0/E. Highway Pavement
Sub Base:
- Ensure that approved sub-base course material is used and the material sample shall be collected and tested as per project specifications upon receiving of material at site.
- Thickness of sub-base course shall be 200mm as specified in the approved drawings, and it shall be placed in two layers.
- Sub Base material spreading shall be started after receiving the compaction test results of Sub Grade.
- Sub-base material loads shall be spread outside area on which it is spread to ensure that no segregation occurs and it shall be spread evenly using a grader to maintain the levels and thickness of layers.
- Each layer shall be must be compacted to an average of 100% of MDD with no single value below 98%
- Minimum field density tests shall be one test for every 300 Sq.meter of granular sub-base laid
- Minimum material test requirement shall be one sample for every 1000 cum of material and test shall be as follows grading, plasticity index, sand equivalent, MDD, and CBR, loss by abrasion by the approved laboratory as per the project specifications.
Aggregate Base Course:
- Ensure that approved sub-base course material is used and the material sample shall be collected and tested as per project specifications upon receiving of material at site.
- Thickness of sub-base course shall be 150mm as specified in the approved drawings.
- Aggregate base course material spreading shall be started after receiving the compaction test results of Sub Grade.
- Aggregate base course material loads shall be spread outside area on which it is spread to ensure that no segregation occurs and it shall be spread evenly using a grader to maintain the levels and thickness of layers.
Prime Coat:
- • Ensure that approved material is used and each consignment test certificate for prime coat (MC 70) shall be provided.
- Prime coat shall be tested as per project specifications.
- Prime coat shall be applied between road base course and bituminous base course as per approved drawings.
- The same shall be cured for a curing period of 48 hours prior to laying of bituminous base course.
- Bituminous material for the prime coat shall be applied in quantities of at least 0.7 ltr/m2 not exceeding however 1.50 ltr/m2.
Bituminous Base Course or Binder Course
- Ensure that approved Bituminous base course material is used and each consignment test certificates shall be provided for Asphalt cement used (AC 40-50).
- Bituminous base course shall be of thickness 90mm as per approved drawings.
- Bituminous base course shall not be placed during dusty, foggy and Rainy weather.
- Bituminous base course material shall be transported in trucks from hot mix plant & its final placement temperature shall not be less than 150 oC
- Consistency of mixture shall be checked for each 200 tons.
- Site engineer in coordination with surveyor must ensure laying of bituminous course to the correct levels and to the specified longitudinal and cross section profiles.
- The Bituminous base course shall be evenly placed by mechanical spreader on a clean base in a manner that it does not become segregated.
- The seams of the bituminous base course shall be sufficiently staggered against each other and it should be executed straights, longitudinal if necessary being adapted to the road alignment.
- Bituminous base course shall be compacted evenly over the entire surface by using pneumatic & steel roller.
- Gradient slope shall be maintained as per approved drawings.
- The core sample to be taken after compaction to determine the layer thickness and the MDD as per project specifications.
Tack coat:
- Ensure that approved material is used and each consignment test results shall be provided for Tack coay (SS l-h).
- Tack coat shall be tested as per project specifications.
- Tack coat shall be applied between bituminous base course and the wearing course as per the lFC drawings.
- Tack coat shall be cured for at least I hour.
- Tack coat shall be applied in quantities of at least 0.3 ltr/sqmtr, not exceeding, however 0.60 ltr/sqmtr.
Wearing Course or Surface Course:
- Ensure that approved material is used and each consignment test certificates shall be provided for Asphalt cement used (AC 40-50).
- Temperature of mixture to be measured at site and it should not less than 150°C.
- Consistency of mixture shall be checked for each 200 tons.
- Thickness of wearing course shall be 60mm as per approved drawings
- Wearing course shall be placed in one layer above the bituninous base course and one coat of tack coat shall be applied between bituminous base course and wearing course.
- The Wearing course shall be evenly placed by mechanical spreader on a clean base in a manner that it does not become segregated.
- The seams of the wearing course shall be sufficiently staggered against each other and it should be executed straights, longitudinal if necessary being adapted to the road alignment.
- Wearing course shall be compacted evenly over the entire surface by using pneumatic & steel roller.
- Site engineer in coordination with the surveyor must ensure the top levels and slope is maintained as per approved drawings.
- The core sample to be taken after compaction to determine the layer thickness and the MDD as per project specifications.
Temperature:
- Temperature shall be checked whenever material is delivered to site.
- Aggregate ingredient shall be heated to a temperature between 160°C to 179°C.
- Asphalt cement shall be heated to a temperature between 146°C and 156°C at mixing time.
- All bituminous mixtures shall leave the paver at a temperature not Jess than 150°C.
- Prime coat (MC-70) between 50°C and 80°C.
- Tack Coat (SS-1 or RS-I) between 10°C and 50°C.
Joints:
- Longitudinal Joints in asphalt courses shall be offset by 300mm in relation to the longitudinal joints of the underlying course
- Transverse joints in succeeding layers shall be offset by at least 2m. The same shall apply when new pavement is laid in contact to an existing, which will be cut back in steps, 2m wide in each of its layers
- At transverse joints the previously laid work shall be cut to a vertical edge. Before laying the material against it, the vertical edge to be painted with hot bitumen
- Minimum number of joints to b exercised/considered during execution
Compaction of Mixtures:
- After spreading and strike-off, the rolling operation by pneumatic and stell roller shall star immediately and shall operate as close as possible to the paver without excessive tearing.
- Rolling will not be prolonged till cracks appear.
- The asphalt layer shall be compacted to a minimum degree of 98% of compaction.
Thickness of Cores:
- Depth of each bituminous paving course shall be measured by cored samples.
- Samples shall be one sample for 600 sqmtr.
- Cored sample shall be 10cm in diameter (nominal)
Surface Tolerances:
Non Bituminous Courses:
The thickness and cross section as shown on the approved drawings shall not vary more r
than -5mm to +10mm from the required elevations.
Bituminous Courses:
Maximum variations allowed for 3m shall be:
- Base Course = 4mm
- Wearing Course = 3mm
Road Markings:
- Road markings shall be applied wherever necessary or as directed by ADWEA to control and direct the traffics.
- Road markings shall be marked by thermoplastic as per project specifications.
- Road markings shall be sprayed on the road in an even thickness of 2mm.
Inspection and Testing:
- Each activity like backfilling of Sub grade and Sub base, In situ Density test for Sub base & Sub grade and laying of Bituminous base course and Wearing course work shall be intimated to 0/E through inspections.
- After due completion of laying of Asphalt work shall be offered to 0/E’s inspection and comments on the work shall be rectified and notified for re-inspection if any.
- Testing of each consignment delivered to the site shall be carried out as per the specifications for road works.
Conclusion:
Full article on Method Statement for Asphalt Paving Works | Asphalt Concrete | Asphalt Pavement Construction | Asphalt Road Construction | Highway Pavement. Thank you for the full reading of this article in “The Civil Engineering” platform in English. If you find this post helpful, then help others by sharing it on social media. If you have any question regarding article please tell me in comments.
2 Comments
AoA Waseem bhai,
Kindly send me these Method of Statement formats on my email. I will be very thankful to you.
Thanks for the comments please visit more articles by clicking on “All Posts” tab of the Menu Bar